Selecting the Power Tool to Suit the Joint
To help ensure that you achieve the Torque accuracy required of your application, it is important to select a power tool with low scatter and low mean shift. Joint stiffness varies, so it’s necessary to make an allowance for it to achieve the proper torque.
Fitting screws into steel without interlining components is one example of a hard joint with rapid tightening. For this application, the power tool needs to have a quick clutch that interrupts the torque at the preset level.
Another example is a soft joint with gaskets and washers, or a long screw, requires a screwdriver with a strong motor to attain short tightening times.
If there are subsidence or plastic deformations in the joint, then you should opt for a clutch type power tool or a tool with a hydraulic pulse mechanism. The joint would then have time to settle as you are assembling.
Joints with self-locking elements in the thread or clamped nuts are becoming increasingly common. If you work with joints like this, we recommend a screwdriver with a shut-off clutch.
To fully utilize the high performance of a quality power tool, it’s important to know the demands made on the power tool by different screwed joints. Here are some examples that will help you select the kind of power tool you require.
Machine Screw – Hard Joint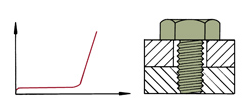
Low resistance to turning until the screw head reaches its seating, after which resistance rapidly increases. For rapid screw driving with moderate Torque accuracy choose a high speed tool. For close torque limit or when the quality of thread is uneven, choose a lower speed tool. This is also recommended for brittle material. The most suitable clutch is a shut-off type. An alternative choice is a slip type.
Machine Screw – Soft Joint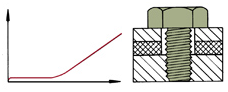
Low resistance to turning until the screw head reaches its seating, after which resistance slowly increases. A slower and more powerful tool should be used to seat the fastener properly to minimize relaxation in the joint. Most suitable clutches: Shut-off type. Slip type possible.
Self-Drilling Screw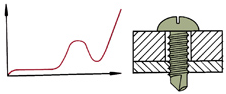
The turning resistance gradually increases during drilling and thread cutting, but more slowly than with self-threading screws. Choose a tool with speed over 1000 RPM. A slip type clutch is generally suitable but for thin material choose shut-off.
Machine Screw – Locking Element in Thread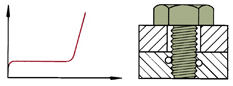
Relatively high resistance to turning before screw head reaches its seating after which resistance rapidly increases. Choose a tool with high Torque from the lower speed range. If rapid driving is required choose a larger tool with a higher speed. Suitable clutches: Shut-off and slip type.
Thread Producing Screw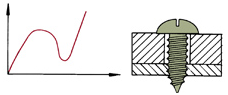
The turning resistance gradually increases as the screw is producing the thread and reaches a maximum just before the entire hole is threaded. Choose a tool within speed range 800 to 1300 RPM. Slip type clutches are generally suitable, but for thin material choose shut-off type.
Wood Screw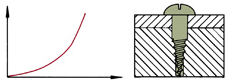
The turning resistance gradually builds up as the screw is being driven and increases rapidly when the screw head reaches its seating. The process varies considerably with the degree of pre-drilling, different type of wood and sizes of screw. Choose a low-speed tool, 400 to 800 RPM. Suitable clutches: Slip type and direct drive.
Source by: Mountz